Innovation in Ecogate's New greenBOX Hardware
- David
- May 25, 2023
- 7 min read
Updated: 5 days ago
Listen to this article
Cutting-Edge Software Deserves State-of-the-Art Hardware

We recently covered the cutting-edge software our new generation of greenBOX Control Units are using (which we cover in depth here). Today, we’ll be diving into the hardware innovation behind the brain of an Ecogate On-Demand Industrial Ventilation System.
The next generation of greenBOX Control Units are redesigned from scratch, combining robust hardware with state-of-the-art software. Not only can a single unit manage multiple dust, fume, and mist collection systems, they’re also more cost effective.
Moving away from conventional industrial control computers loaded with numerous Modbus communication ports, we've designed our own interface specifically suited for on-demand ventilation systems. This has enabled us to use any industrial computer, substantially reducing hardware costs. The following sections elaborate on the enhancements we've made to our control units' hardware design.
greenBOX Max and greenBOX Master Designs
The Enclosure Design: Cutting-edge Without Cutting Corners
Most industrial control systems are housed in ordinary gray or black boxes. But our team, motivated by the sleek innovation of David Vera's ‘cutting edge’ design, chose to break this mold. The sharp aesthetic in our new control unit enclosures is actually already incorporated in our gate bodies and gate motors - even our Volt Sensors have that 'cutting-edge' - check them out in the gallery to the left.
The result? An unmistakable Ecogate design that distinguishes us in the industry (interestingly, we later observed a similar shape outline in the layout of Tesla factories - shown below). Each custom-made enclosure, while being visually appealing, also serves its functional purpose efficiently. The design aligns with our core philosophy, reminding us that "Industrial Energy Efficiency" is our foremost pursuit.

Tesla Factory
Wired Modbus vs Wireless Systems
In developing our new family of greenBOX control units, we considered incorporating wireless communication between control systems, gates, and Variable Frequency Drives (VFDs). At first glance, eliminating the need for gate wiring seems beneficial. However, after a thorough cost analysis, we found the wireless system to be more expensive.
This was mainly because, even without the gate wires, power still needs to be supplied to both the gate and the wireless transmitter. While it's feasible to install this within the electrical box of the workstation following the National Electrical Code (NEC 70), it comes with complications. Doing so could void the machine warranty and finding safe space for the power supply can be challenging. In addition, every machine requires a unique, and therefore costly and time-consuming, installation process.
The diverse power requirements of workstations, with some using 115V or 230V AC and others 460 or 575 V AC, present additional difficulties, necessitating different solutions for each scenario.
An alternative is to connect the power supply to a general 120V AC outlet. But this too poses problems. Many machine locations lack available outlets, installing new ones can be expensive, and the power supply becomes prone to damage in such locations due to the harsh industrial environment.
America and Europe
Moreover, American factories are usually much larger than those in Europe, leading to the need for repeaters to ensure reliable wireless communication across larger areas. This inevitably increases system costs and complicates maintenance. In Europe, all devices used at factory installations must be Electromagnetic Compatibility (EMC) tested per CE standards. In contrast, in the US, only wireless communication devices need FCC standard certification. For example, in Europe, Variable Frequency Drives must be installed with EMC filters, while in the US, VFDs are installed without these filters. This makes it difficult to achieve reliable system operation because interference levels are higher in US factories.
Our Solution
The greenBOX acts as the power supply for the gates, and a single cable serves for Modbus communication to the gates and their power supply. The process is as simple as connecting four terminals at each gate (the cable is daisy-chained from gate to gate). This approach showcases the genius of simplicity in our design, providing a cost-effective, reliable, and straightforward solution to the complex challenge of managing industrial ventilation systems.
Hardware Upgrades to the "Next Unit of Computing"
Like the rest of the world during the Covid-19 pandemic, Ecogate faced major supply chain challenges. We experienced a shortage of industrial panel PCs from Advantech, which we had been using in our previous generation products, for a staggering two years. To make matters worse, Texas Instrument ARM microprocessors were unavailable for three years. The list of unavailable electronic components seemed never-ending.
To overcome these supply chain issues, we took matters into our own hands. We designed our own interface board with RS485 Modbus RTU ports, allowing the new greenBOX software platform to be compatible with any industrial x86 computer. After careful consideration, we opted for the "Next Unit of Computing" (NUC) designed by Intel Industrial in standard format.
Powerful Processors
The NUC computers are equipped with the latest powerful yet efficient processors, making them an ideal choice for the greenBOX control unit. These modern, powerful processors enable a single control unit to control an incredibly vast number of industrial ventilation systems. Moreover, the low heat emissions of the NUC computers enhance the overall efficiency of the control system and simplify the enclosure cooling. To ensure adaptability and ongoing efficiency, we increased the memory capacity and expanded the SSD disk space to accommodate future software updates.
Production Flexibility
By choosing an industrial NUC computer, we benefit from multiple suppliers, such as Intel Industrial and ASRock Industrial, who produce these computers in a standard, replaceable format. This ensures greater availability and flexibility for our production needs. These suppliers are very fast in adopting new Intel and AMD processors, therefore in the future we will benefit from the use of more powerful processors that will use less power.
To sum up, we’ve tackled the supply chain challenges brought on by Covid by creating our own Modbus interface board and adopting the reliable and powerful industrial NUC computers. These strategic decisions not only address the availability issues but also offer improved performance, energy efficiency, and expandability for our greenBOX control units.
Open/Close Enclosure Designs
Enhanced Reliability Through High-Performance Power Supply Redundancy
We're thrilled to introduce a new element of reliability to our larger control units, the greenBOX Max and greenBOX Master models: a redundant power supply.
Drawing on a quarter-century's worth of expertise in implementing dust collection control systems, we've consistently surpassed industry standards for system dependability. Nevertheless, we've observed that power supply failures have been the most prevalent issue impacting control units and gates.
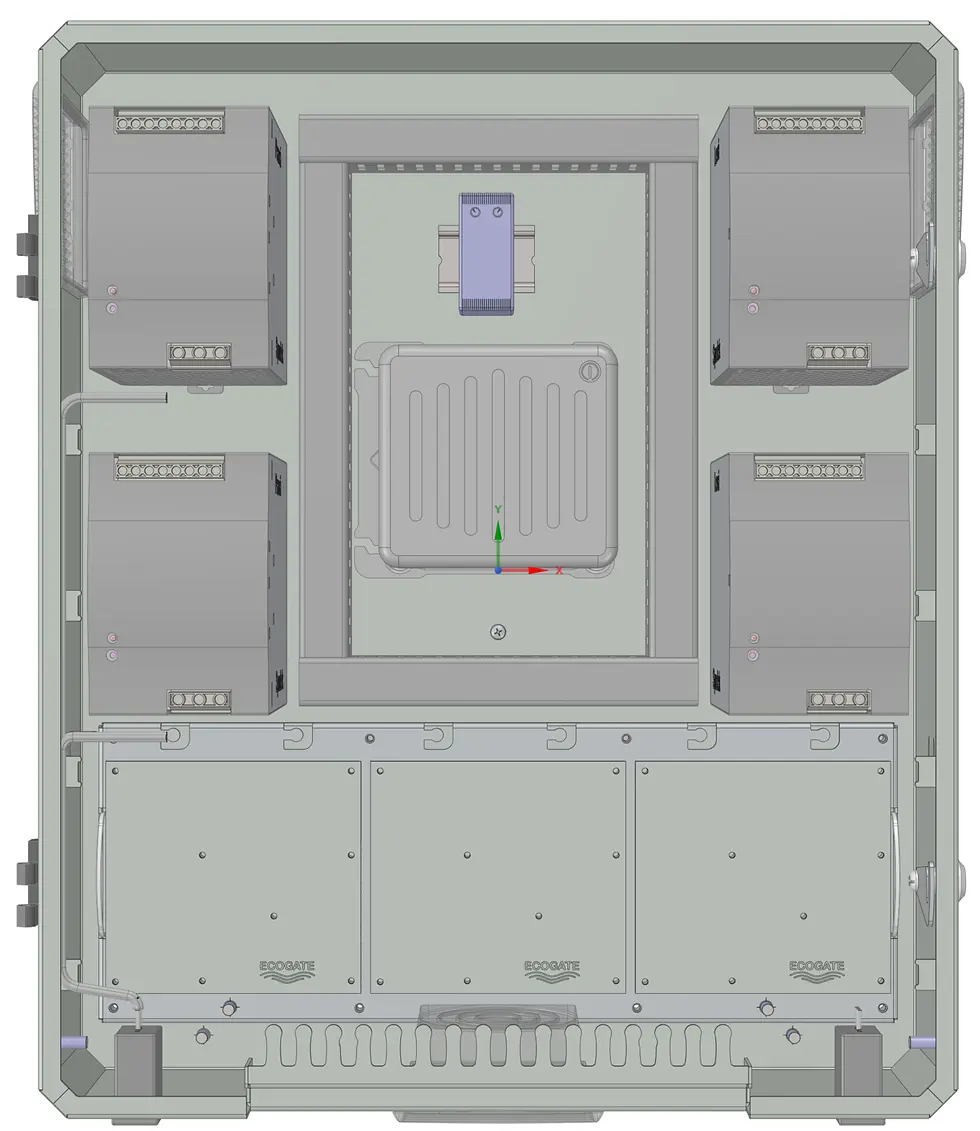
More Power
To tackle this, we've engineered a dual high-end redundant power supply system for our new larger control units, the greenBOX Max and greenBOX Master. Each unit is outfitted with two identical top-tier industrial power supplies. Boasting a staggering 94% efficiency, active power factor correction, and a Mean Time Between Failures (MTBF) of 1 million hours, these systems demonstrate extreme efficiency and longevity.
The concept is straightforward: if one power supply fails, the other takes over seamlessly, ensuring continuous operation. Simultaneously, the greenBOX alerts local maintenance staff to address the faulty power supply.
The Value of Backup Power
There may be some who question the necessity of such a high-end feature. Yet, consider that our Ecogate systems service large-scale clients, such as largest factories in woodworking and pharmaceutical plants. A halt in production here can result in millions of dollars in losses, or even necessitate the disposal of entire batches if dust collection is interrupted mid-process in a pharmaceutical factory. Moreover, with thousands of systems installed worldwide, even a minuscule percentage of power supply failures equates to numerous compromised systems. With these stakes, we believe our dual power supply approach isn't just desirable—it's essential.
Modern User Interface via a Striking OLED Display
A product's aesthetic often forms the initial bridge to user engagement, paving the way for an enjoyable system experience. Recognizing this, we've designed sleek industrial enclosures and an intuitive, appealing software user interface. To truly do justice to our user interface, we've employed state-of-the-art Samsung OLED displays in our greenBOX Max and greenBOX Master enclosures.
Low Power, Exceptional Brightness
OLED displays have made a name for themselves in high-end televisions and premium laptops, admired for their ability to render a spectrum of rich colors while sustaining the highest contrast ratio across all display technologies. They do this whilst still ensuring exceptional brightness. Furthermore, these displays are an ideal pick for industrial applications, displaying especially low power consumption when paired with a dark user interface, as is the case with Ecogate. This is due to the fact that dark pixels consume no power—a marked difference from LCD panels that require constant backlighting, thus consuming more energy.
Display Lifespan
Admittedly, OLED displays do present a challenge: they typically possess a shorter lifespan than other display technologies, particularly when displaying a static image over long periods. Yet for us, this issue is of minimal concern, as our greenBOX control system is primarily accessed remotely, and the display is infrequently left on for extended periods. In fact, our screensaver functionality switches off the display following roughly ten minutes of inactivity, and a simple screen tap promptly revives the display.
Integrating Electronic Fuses for Superior Safeguarding in greenBOX Control Systems
We're introducing electronic fuses into our greenBOX control units for the first time, offering several notable benefits over conventional fuses. The most prominent of these benefits is an upgrade in safety measures: the swift disconnect of electronic fuses during fault situations significantly improves the safety specifications of the greenBOX control systems. Notably, these electronic fuses are implemented in cutting-edge cars, like those produced by Tesla, setting them apart from other manufacturers like Ford who have yet to adopt this technology.
Electronic vs Conventional Fuses
Electronic fuses outperform conventional fuses by reacting swiftly in overcurrent scenarios, disconnecting the power circuit in a matter of microseconds. This rapid response is crucial to avert damage to the 24V DC power supply and interface. Our design supports programmable trip current, empowering users to establish their preferred current threshold based on system configuration.
Contrary to conventional fuses that necessitate replacement after being tripped, electronic fuses reset themselves automatically or can be manually reset through the User Interface. This characteristic reduces downtime and maintenance work. Moreover, electronic fuses have a more compact design, conserving space on the Ecogate interface board and in turn, cutting costs.
In our greenBOX control units, the integration of electronic fuses enhances performance, safety, and dependability of dust, fume, and mist collection systems.
People, Profits, Planet
The new generation of greenBOX Control Units is set to redefine Industrial Energy Efficiency, and we area thrilled to bring that to the world. At Ecogate, we'll continue to develop cutting-edge technology that benefits the People, increases Profits and helps the Planet - without cutting corners ;)
Author, Ales Litomisky
Comments